Rotary kiln incinerator flue gas treatment process plan
The incineration treatment can solve the dangerous waste in a huge level and harmless treatment. At this stage, about 90% of the national hazardous waste treatment and management centers have selected the hazardous waste incineration treatment system software. The soot is heat-transferred by the waste heat boiler to generate steam. Because of the low quality of the steam, in the traditional technical control, the company except for its own use, the vast majority of air pollution, not only causes air pollution, but also leads to a large waste of power energy. The resulting steam power generation will be connected to the kinetic energy ladder, and the improvement of power and energy utilization has become a difficult problem to be considered in the development trend of the hazardous waste manufacturing industry.
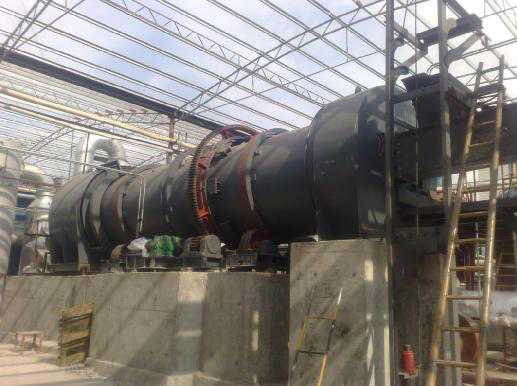
In most hazardous wastes suitable for incineration treatment (such as paint residue, chemical plant residue, waste chemical, etc.), S, Cl, F and other components are included. The hazardous waste incineration treatment project stipulates that the hazardous wastes should be classified, averaged and sent to the incinerator for incineration; the incineration treatment should be considered to consider the pollutant discharge index value, which is the normalized treatment system software and flue gas purification of the project. The system software clearly proposes higher production process regulations.
Hazardous waste incineration treatment technical standards
1) The incinerator dust waits for more than 2s at around 1100 °C.
2) The moisture content of oxygen in the inlet and outlet of the incinerator is 6% to 10% (gas).
3) The burnout removal rate is ≥99.99%.
4) Ignition high efficiency ≥99.9%.
5) The thermal burning rate of incineration treatment sediments is <5%.
6) The system software in the operation of the incinerator is under air pressure to prevent harmful substances from escaping.
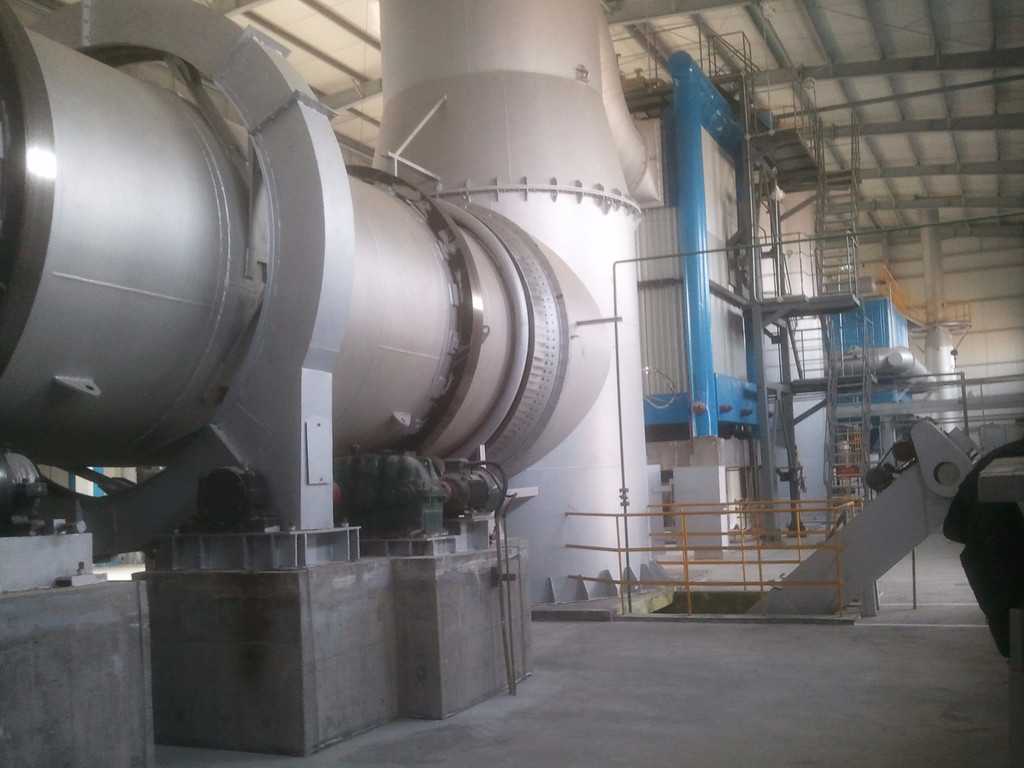
7) Exhaust gas purification equipment, alarm equipment and emergency solution equipment are installed under the incinerator.
8) Incineration treatment workshop work system: implementation of four shifts and three operations, 8 hours in each shift.
9) Incineration treatment workshop design concept service project period 20a, critical machinery and equipment incinerator application period exceeds 15a.
10) The environmental protection standard for soot and dust is implemented in the Code of Practice for Environmental Pollution Control by Dangerous Waste Incineration.
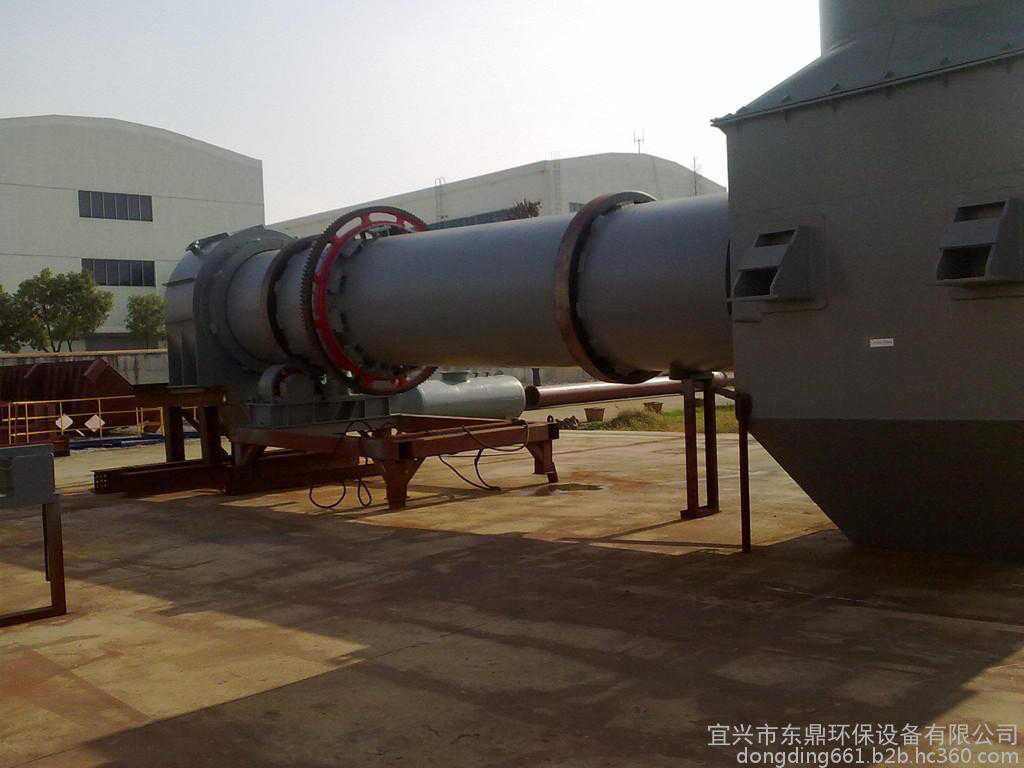
3 flue gas treatment processing technology for hazardous waste incineration treatment project
For smoke solutions with nitrogen oxides
At this stage, there are two key points for this flue gas purification solution with nitrogen oxides: a selective non-reduction method and a selective catalytic reaction reduction method. There is a necessary difference between the two, and the key depends on the metal catalyst used in the application.
Among the key applications of the selective non-reduction method is V2O5 or TIO2 for the necessary level of catalytic reaction and cleaning, so as to keep the NOx emission level to 50 mg/m3; and the selective catalytic reaction reduction method is based on the application. The oxidant NHOH or the urea solution (NH2)2CO is used for the purpose of reducing the concentration of the sewage concentration, and the specification of the water content reduction is not higher than 20 mg/m3. Although the cleaning method using the selective catalytic reaction reduction method is more effective, the cost of consumption is relatively high, and thus the technical application range is relatively small.
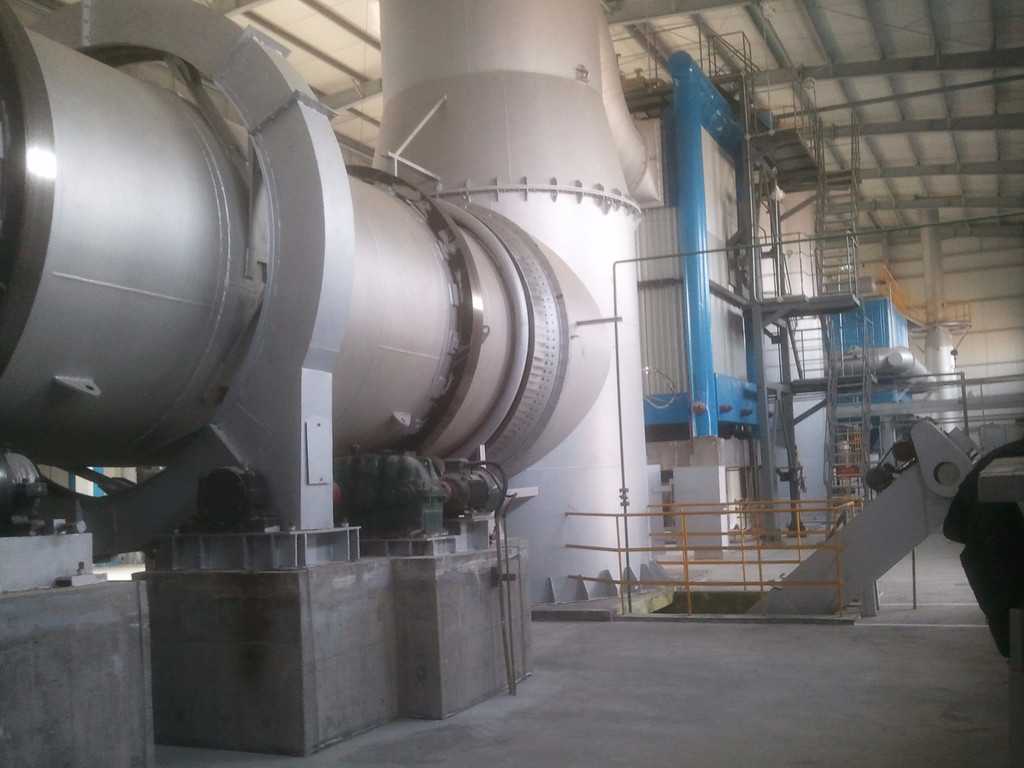
Metal cadmium, dioxins
Firstly operate the "3T+1E" standard of the second combustion chamber of the incinerator, that is, ensure sufficient temperature (rotary kiln incinerator > 1100 ° C), sufficient waiting time (> 2 s at 1100 ° C in rotary kiln incinerator), sufficient excitation (The second combustion chamber throat is ignited by the re-wind or the burner to make the cyclone swirling), and the excess capacity is sufficient. Secondly, the forced self-spraying and desuperheating method is adopted to reduce the temperature from 550 °C to 200 °C in 1 s, bypassing the regenerating section of dioxins.
In the general dioxin removal process composition, the key function of dioxin removal is the effect of activated carbon filtration, taking into account the idea of suppressing the conversion of dioxin, in order to exceed the stronger dioxin to remove the actual effect, Try not to use an electrostatic precipitator. In order to reduce the investment in machinery and equipment projects and simplify the processing technology, it is possible to remove the metal cadmium and dioxins by spraying the activated carbon powder before the bag filter. Some metal cadmium has volatile matter, and most of it enters the dust during the whole process of ignition, and is sucked on the dust during the whole process of dust reduction, in the whole process of removing acid and alkali vapor and removing ash. Was removed.