Rto regenerative incinerator
Product introduction
The rto regenerative incinerator is a high-efficiency exhaust gas purification machine whose principle is to heat industrial waste gas to 760-850 °C to oxidize and dissolve organic waste gas (VOCs) in organic waste gas into CO2 and water.
The calorific value caused by the whole process of air oxidation is stored in a specially-made porcelain regenerator, and the regenerator is heated to "storage". The heat stored in the body of the porcelain regenerative heat is used to heat the industrial waste gas that the event enters. The whole process is the whole process of the “exothermic reaction” of the porcelain regenerator, thereby saving the cost of the whole process of organic waste gas warming.
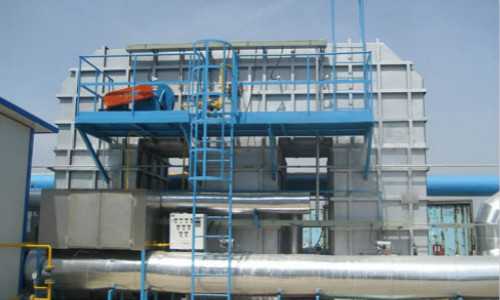
Technical basic principles:
The industrial waste gas is heated to about 760 degrees Celsius to convert the VOC in the organic waste gas into CO2 and water in the air. The high-temperature vapor caused by air oxidation flows through the specially-made porcelain regenerator to warm the porcelain body and "storage heat", which is used to heat the industrial waste gas that the event enters. In turn, it saves the cost of organic waste gas to raise the temperature. The porcelain regenerator should be divided into two (including two) zones or chambers, and each regenerator will experience the procedures of heat storage-exothermic reaction-cleaning, and reciprocate and continue to work.
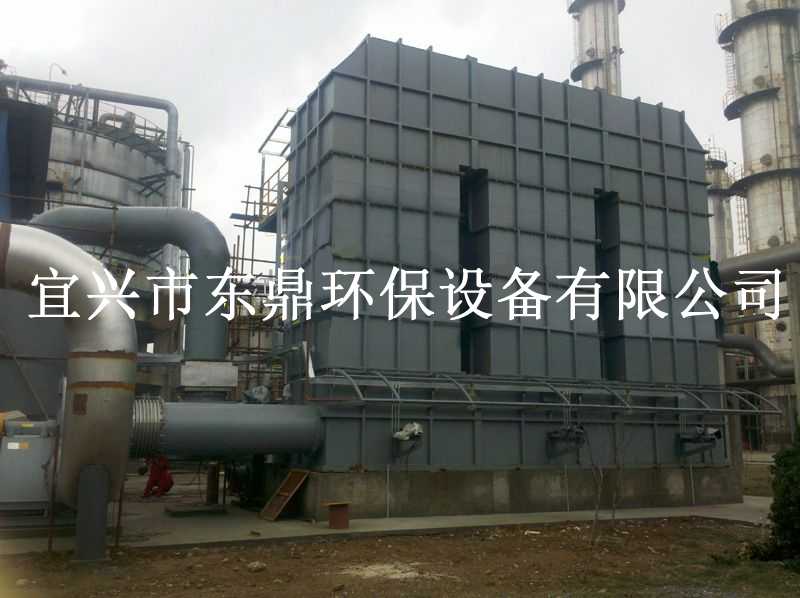
System software features:
1. The regenerative heat transfer equipment is selected, the heat storage plasmid carrier and the vapor body are immediately transferred, the temperature of the radiation source in the furnace is large, and the heating is faster; the ultra-low temperature heat transfer effect is remarkable, so the heat exchange effect is very high.
2. The heat storage room temperature leveling classification is upgraded, which improves the heat conduction in the furnace, and the actual effect of heat transfer is more. Therefore, the air oxidation furnace of the same mud production volume can be reduced in size, which greatly reduces the engineering cost of the equipment.
3. Expanding the high-temperature flame air oxidation area, the boundary of the flame is basically extended to the limit of the furnace, and then the temperature inside the furnace is symmetrical, which not only improves the cleaning efficiency, but also increases the service life in the furnace.
4. The temperature in the room of air oxidation is generally rising and spreads more and more uniformly; the temperature in the furnace reaches 760~800 °C, the cyclone rate is small, the air oxidation is faster, the high temperature waiting time of the soot in the furnace is long, and the organic compound is oxidized and dissolved by air.
5. The system software adopts PLC automatic air oxidation operation, high level of automation technology, stable operation and high reliability of safety;
6. According to the condition of organic waste gas, energy setting equipment can be effectively set up, heat exchanger, heat transfer oil boiler or waste heat boiler can be connected in high temperature air oxidation chamber; ultra-low temperature smoke is used to warm organic waste gas, and waste heat recovery in organic waste gas can be flexibly used.
System software technical characteristics
The performance double seal is used to improve the valve, the external leakage rate is 0, and the high efficiency of all system software is about 99%;
Due to the selection of performance imported regenerator, the organic waste gas treatment is more complete, high efficiency, environmental protection and energy saving, up to standard discharge;
Rated value of total cleaning flow selection range: to solve the exhaust air volume from 3000-100000Nm3 / h, ignition, no pollution, high heat transfer efficiency;
The grade classification is used to ignite the technicality, the temperature in the regenerative room is symmetrical, the heat transfer is good, and the treatment rate is about 99%;
The energy can be comprehensively utilized, reducing the operating costs of machinery and equipment, and the repair rate is low. The machine and equipment maintain remote control and control, face-to-face maintenance monitor;
Fuel usage
When starting the burner, it is a large output; when it is in normal operation, it is clear according to the organic exhaust gas concentration value. When the concentration value is about 2000mg/nm3, the ignition can maintain the thermal cycle in the furnace and zero energy consumption;