Waste water incinerator
Features:
1) A tangential atomizing device (internal hybrid two-fluid atomizer) is used. The mixing degree, atomization effect, burning rate and efficiency are extremely high, the excess coefficient is low, and the combustion is sufficient.
2) The eddy current effect is good. The combustion retention time is more than 2 seconds, and there is no dead angle in the combustion.
3) High combustion safety. The control logic program has the function of not igniting the flammable and explosive gas before ignition in the furnace.
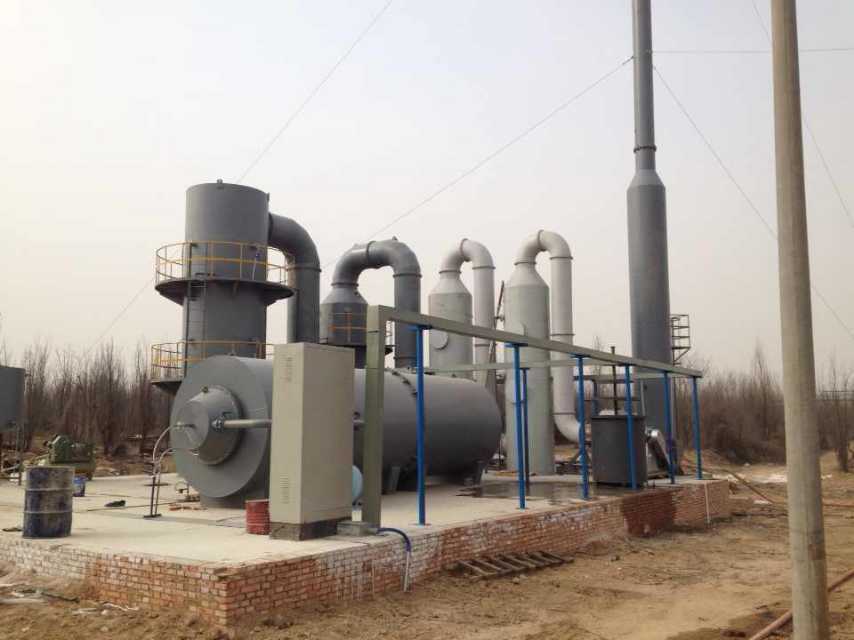
4) According to the composition and characteristics of the wastewater, design the incinerator body with different shapes and lining. According to the salt content in the wastewater, different furnace temperature control is designed to ensure that the inorganic salt is not hanged in the furnace when it is incinerated, and few salt mists are emitted outside the furnace.
5) Fully consider the use of waste heat after wastewater incineration.
6) Waste water and waste solvent can be processed at the same time to waste waste and reduce operating costs.
Scope of application:
1. High concentration (BOD, COD) wastewater, waste liquid, organic acid, organic alkali, etc.
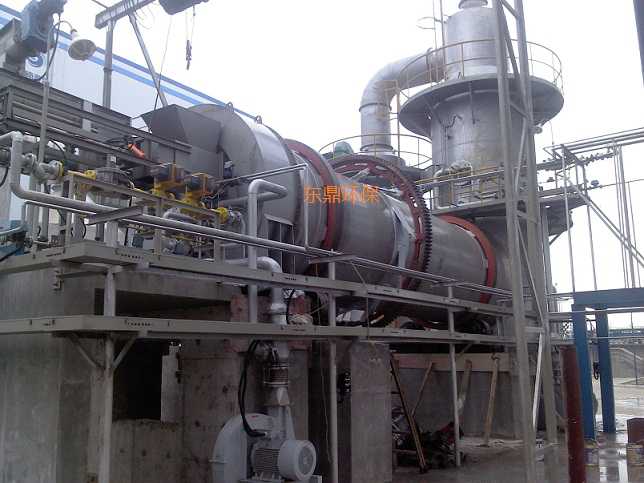
2. Low-salt wastewater, etc.
3, the general processing capacity is: 50kg / h ~ 2000 kg / h
Scope of application:
Incineration residue, sludge, waste packaging materials, solid salts and solid organic matter, non-flammable high concentration (BOD, COD) wastewater, waste liquid, waste acid, waste alkali, and combustible waste liquid, waste solvent, waste PCB, etc. . Suitable for the production of medicines, pesticides, intermediates, dyes, petroleum additives and additives.
Features:
Atomization, good combustion effect
No secondary pollution Low nitrogen combustion technology, smokeless, odorless, no harmful gases
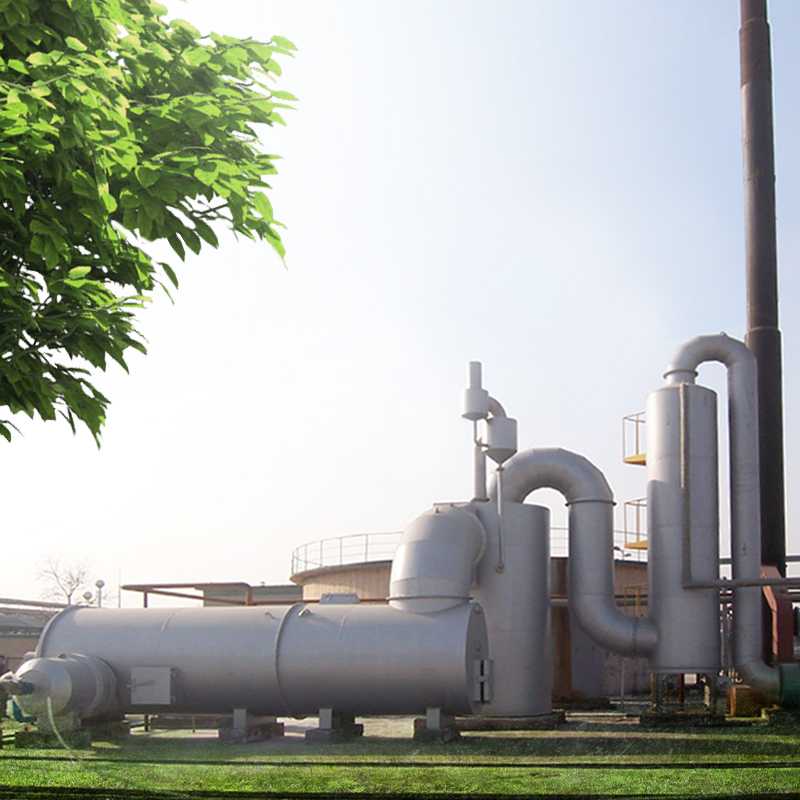
High security, UV monitoring system
Complete alarm system
Low failure rate, use of imported parts for key components
Low operating costs
The incineration exhaust gas purification system consists of a quenching tower, activated carbon injection, dry powder absorption, bag filter, (high efficiency filter), wet deacidification and defogging, and flue gas reheating device. Quenching is to use a spray system to rapidly reduce the temperature of the flue gas to prevent the re-synthesis of dioxins. A certain amount of slaked lime is sprayed into the flue gas to react with the acidic substances in the flue gas, and the water is controlled to achieve a "spray drying" reaction process. The semi-dry deacidification reaction product is substantially dry solid and does not produce sewage. A bag filter is used for the particulate matter trapping method in the flue gas. Before entering the bag filter, a certain amount of activated carbon is injected into the flue gas to adsorb harmful substances such as heavy metals and dioxins in the flue gas, and then effectively captured and removed in the bag filter. After the bag is dedusted, the flue gas enters the packing absorption tower for further deacidification treatment, and after defogging, the flue gas reheating system is used to raise the flue gas to above 120° to ensure that the exhaust gas emission reaches the standard.